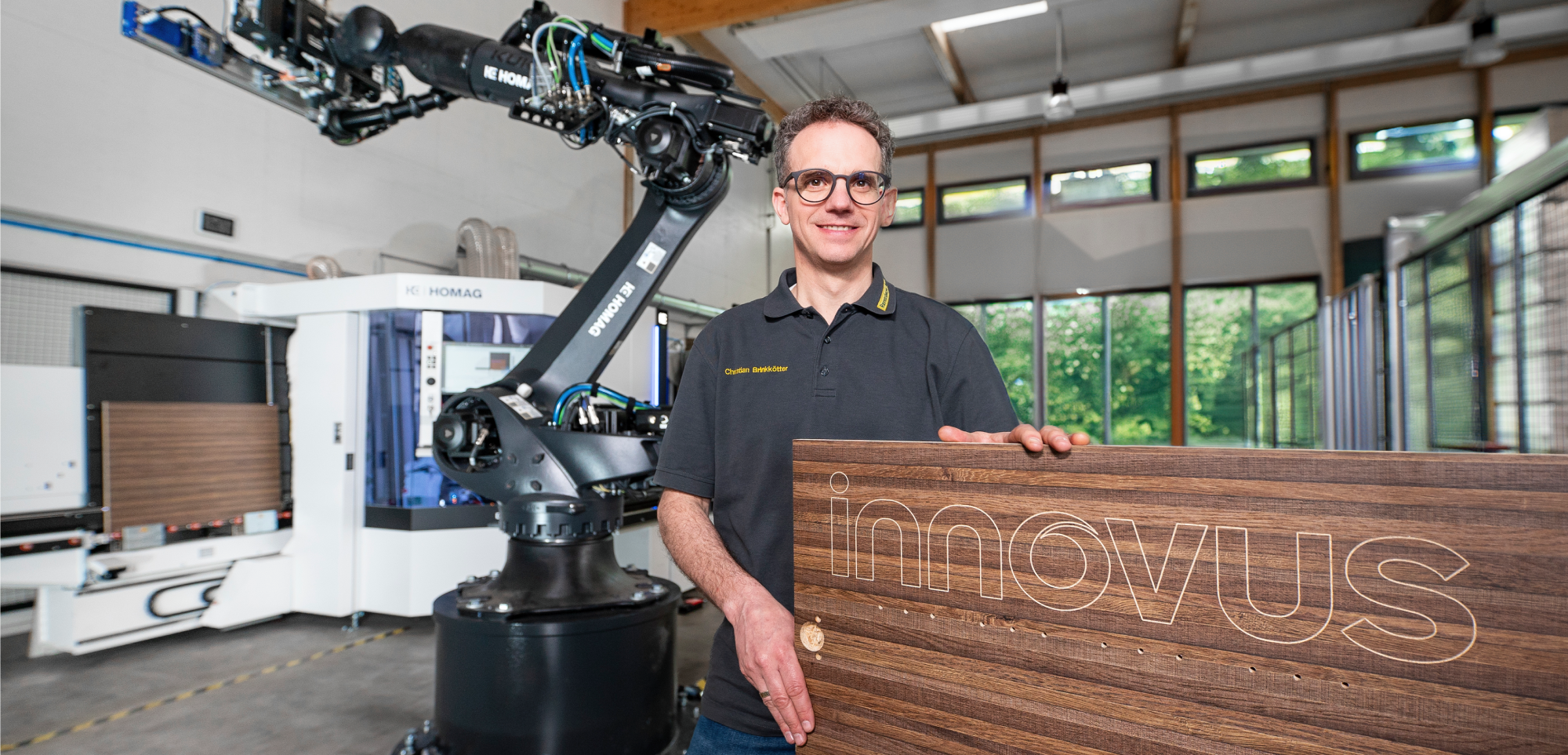
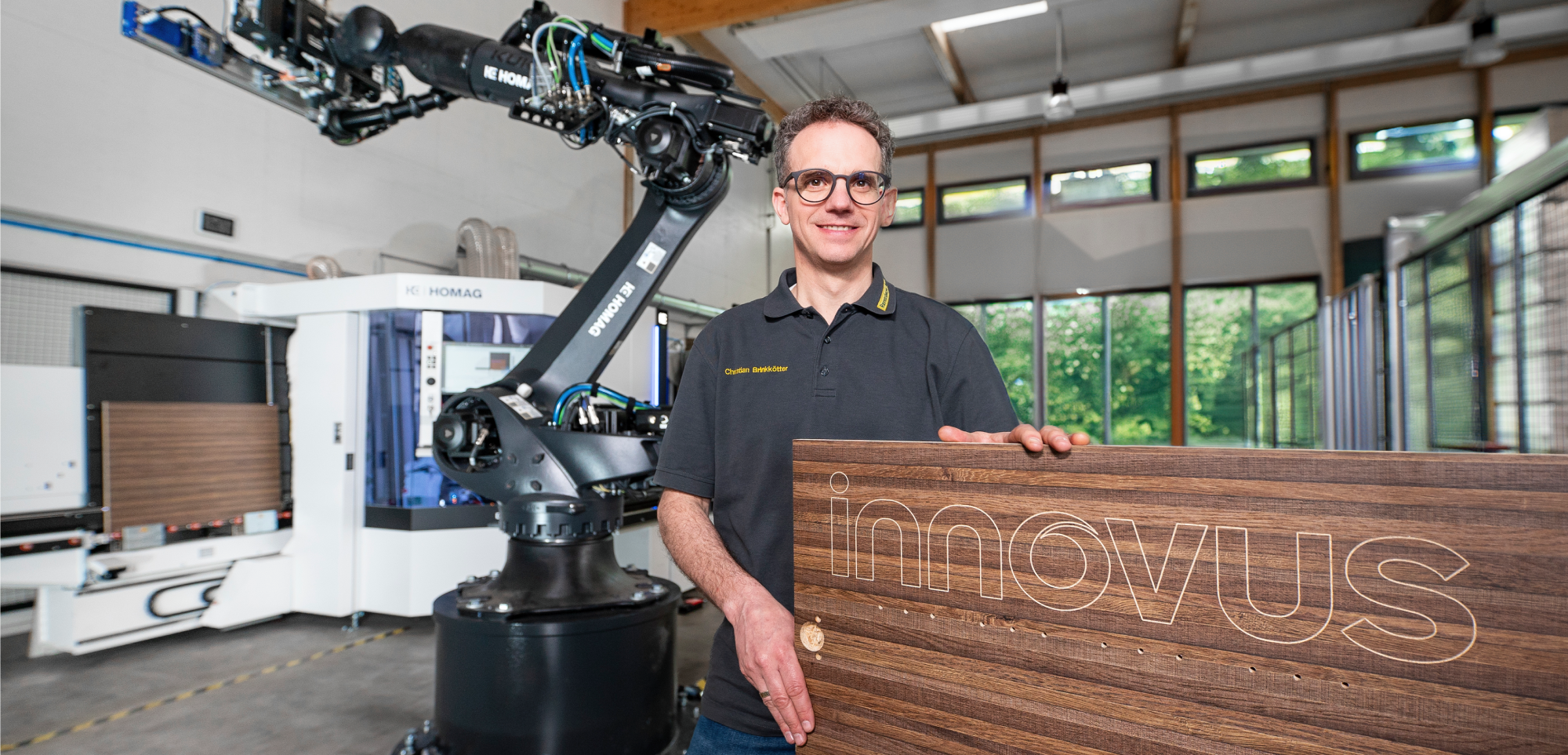
Ravensberger Holz celebrates world premiere with HOMAG and Innovus®
Bielefeld-based timber merchant opts for the latest HOMAG CNC drilling and routing machines with robot support
- Ravensberger Holz GmbH & Co. KG in Bielefeld, Germany, has successfully installed a HOMAG CNC drilling and milling center with robot support for processing Decorative Panels (DP) from Innovus®.
- This innovative solution is intended in particular to support carpentry shops in their daily work in the planning and realisation of individual rooms.
Ravensberger Holz GmbH & Co KG in Bielefeld, Germany, has successfully installed a CNC drilling and routing center with robotic handling, representing a significant step toward automation and digitalization. For HOMAG, the world's leading manufacturer of woodworking machines, this was the world's first installation of the new DRILLTEQ V-310 robotic cell with FEEDBOT D-310 and therefore a true world premiere: “Production is now even more efficient in terms of quality, availability and performance," says Reinhard Maier, Sales Manager CNC Technology at HOMAG.
"With the new solution, we offer our customers even more service - digitised from start to finish," explains Dr. Christian Brinkkötter, Managing Director of Ravensberger Holz. With the help of special software, users can configure, present and order furniture parts according to their individual requirements via the woodworking shop's online portal. This innovative solution is aimed primarily at carpentry shops to support their daily work in planning individual rooms.
Digitisation continues in the fully automated panel warehouse with a capacity of over 10,000 panels. This includes the entire Innovus Express collection of decorative surfaced particleboard from Sonae Arauco for immediate availability. "For an authentic look and feel thanks to unique surface textures," adds Brinkkötter. Finally, the HOMAG FEEDBOT D-310 - for safe, precise and automatic handling of the workpieces - takes over and places the panels in the new CNC drilling and milling processing center: "With our automated processing cell for drilling, routing, grooving and even door processing, it is also possible to produce any type of joint for furniture construction," emphasises HOMAG's Maier.
Once the furniture part has been processed to the customer's specifications, it is packaged and shipped to the customer. "Automation does not stop here - our digital route planning ensures the best possible route optimization and helps us to reduce CO2 emissions. Thinking and acting sustainably is important to the Bielefeld-based timber company, which has had a photovoltaic system since 2001. Demand-driven lighting control, humidification systems, and waste wood recycling to reduce waste are other ways in which the lumberyard is putting sustainability into practice.
Werner Ebenhoch, Sales Manager Trade DACH at Sonae Arauco, sees the installation of the new machine as "a remarkable milestone". He emphasizes that the automated processing of Innovus® panels in the retail trade, which was previously reserved for industrial companies, is "an impressive innovation".
Last but not least, the decorative wood materials from Innovus® play a central role, which also guarantee short distances with the "Made in Germany" label: 100 percent of the wood used comes from sustainable, certified or controlled sources. In addition, 75 percent of the wood is recycled. "Innovus not only feeds our new HOMAG machine, but also supports our concept of sustainable action," says a delighted Brinkkötter.
Related news
01.Related news
Categories